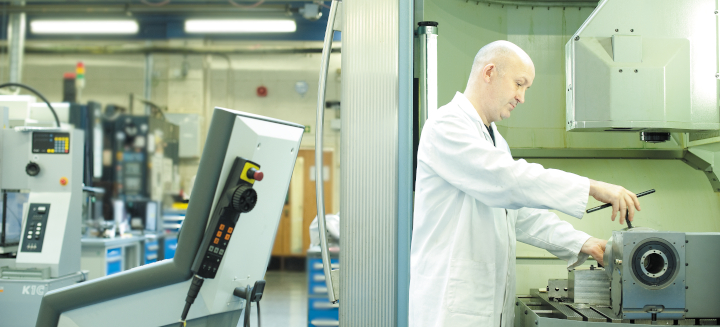
Government and Research Agencies Funded Projects
(Industrial projects not involved)
The MCM team is currently participating in a number of projects funded by Innovate UK, EPSRC and SMART EUREKA CLUSTER. With a total budget of over £12M, the projects show the present commitment to advance technology for robotic on-wing repair, robotics for hazardous environments and advanced manufacturing. Nine MCM staff members and multiple students work closely with Rolls-Royce, SMEs, organisations and universities from around the world to advance the state of the art with real-world applications.
REINSTATE (Repair, Enhanced Inspection, and Novel Sensing Techniques for increased Availability and reduced Through life Expense)
The ATI estimates that through-life engineering services in civil aerospace will be worth $2.5 trillion over the next 20 years. Within the widebody aeroengine market, airliners continue to use long-term service agreements such as Rolls-Royce's TotalCare package. In order to maximise engine uptime and product availability, and to keep the UK at the forefront of this servicing revolution, the eight REINSTATE partners will develop a portfolio of sensing, inspection, and repair techniques for use within on-wing installed engines, in the aerospace maintenance, repair, and overhaul network, and in an array of neighbouring industrial sectors.
Tell me more
Participant organization names:
Funder: Innovate UK
Contact: Dr Abdelkhalick Mohammad
THERMACH (THERmally assisted MACHining of difficult-to-cut materials)
THERMACH project addresses the challenges manufacturing industries are facing when producing components and products of advanced metal matrix composite (MMC) materials. Metal matrix composites, being composed of ductile metallic matrix and hard reinforcement, possess valuable and often critical physical and mechanical properties of highest demand by a multitude of industries. Yet, the same material architecture carries a downside of low production efficiency, high defectiveness of produced parts and associated high costs. Small scale feasibility studies have long demonstrated that these negative effects can be overturned by using hybrid thermally assisted machining processes.
THERMACH advances innovative analytical, software and hardware solutions for Laser Assisted Machining (LAM) and Induction Assisted Machining (IAM) processes to become enabling, competitive and sustainable processes for MMC machining on industrial scale. This is achieved by augmenting the conventional value chain of machining process by smart introduction of satellite tooling, laser, induction and monitoring links. The project also aims to validate and integrate developed solutions in existing production environments of aeronautic, automotive and capital goods industries.
Tell me more
Participant organization names:
Funder: SMART EUREKA CLUSTER on Advanced Manufacturing programme.
Contact: Dr Zhirong Liao
SENSYCUT (Sensor Enabled Systems for Precision Cutting)
Machining is one of the most used processes for producing precision parts used in aerospace and automotive industries. The demand for high performance and quality assured parts requires high precision, often over a large scale resulting in increased manufacturing costs. It has become a rule of thumb that precise machines with stiff structures and large foot prints are required for machining precision parts. As a consequence, machining costs grow exponentially as the precision increases. This has resulted in the development of expensive and non-value adding off-line verification and error compensation methods. However, these methods do not take the impact of cutting tool/workpiece geometry, cutting forces and time variable errors into account. The uptake of additive manufacturing has also resulted in generation of optimised parts often with complex geometries and thin and high walls which require finish machining with long slender tools. In these scenarios, cutting forces can bend the tool and the workpiece resulting in geometrical inaccuracies. Fluctuating cutting forces result in chatter leading to damaged surface integrity and short tool life.
Using new sensors, advanced signal processing and intelligent control systems can provide the ability to detect geometrical and surface anomalies when machining, and provide data to generate strategies to prevent costly mistakes and poor quality. However, off-the-shelf sensors and data transmission devices are not necessarily suitable for monitoring and controlling machining processes. Existing high precision sensors are either too large or too expensive making them only useful for laboratory applications. Conventional statistical and process control methods cannot cope with high data sampling rates required in machining.
The proposed research will realise low-cost sensors with nano scale resolution specific to machining, tools and intelligent control methods for precision machining of large parts by detecting and preventing anomalies during machining to ensure high precision part manufacture and prevent scrap production.
Tell me more
Participant organization names:
Funder: EPSRC
Contact: Dr Zhirong Liao