Research Challenge 3: Controlling connectivity and anisotropy for enhanced functionality
Research Challenge co-leads: Ricky Wildman and Derek Irvine.
AIM: To be able to control the connectivity of additively manufactured objects to enable full functionalization.
The voxelwise approach inherent in AM enables the cost-effective manufacture of highly complex geometries but it can confer anisotropy into the resultant part, as materials must be deposited and then connected. When processing functional materials this can lead to poor inter and intra layer connectivity and functional anisotropy can emerge. Such effects could be amplified in multi-material device production where distinct materials (e.g. dielectric and conductive materials) are sequentially co-printed.
To overcome this, we have modified inkjet formulations to include pre-polymerised material, to improve bonding between successively printed droplets and layers.
Secondary ion mass spectrometry imaging of gold nanoparticles selectively coated onto micro-structures fabricated by two-photon lithography. 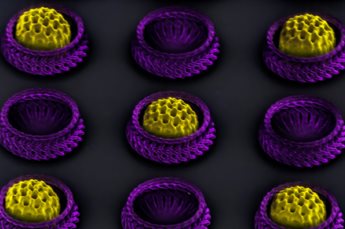
Specifically, hyperbranched polymers have been synthesised, incorporated into printable formulations, and successfully printed, with some advantages over monomer formulations observed. In inkjet and 2PP, these polymers have been shown to enhance processing and improve reactivity. In 2PP, the influences of monomers, photo-initiators, solvent and different laser scan strategies have been systematically investigated. Nanocomposites with functional additives, e.g. graphene and drug molecules, have been demonstrated. By optimising resin formulation and fabrication parameters, enhanced functionality can be achieved.
Inside view of ‘Tocuan’, a bespoke inkjet based 3D printer in UoN that is capable to co-print six different materials. 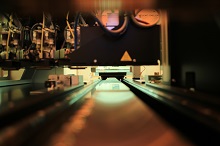
Section of a propeller printed in silver using the new MetalJet drop-on-demand technology 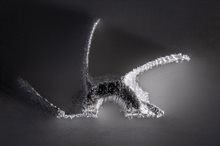
Hyperbranched pDVB stabilised graphene composite powder and ink 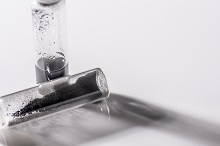
Also, in collaboration with RC4, we have developed a polymer-stabilised graphene dispersion suitable for inkjet printing. This has been used to print conductive tracks for electronic devices in RC4 and the process could be applied to other low dimensional materials. In this research challenge, we also aim to utilise the understanding developed in RC1 and RC2 to optimise interfacial bonding through print strategy and achieve control over microscale properties to realise macroscale functionality in devices as diverse as pharmaceutical delivery systems and electronic circuits.