Drive Stands
Our facilities include rotating drive stands that can power bespoke test units for a range of transmission studies. Each drive stand enables a bespoke research test unit to couple to 1, 2 or 3 shafts. Each drive stand has its own oil and gas systems, as well as DAQ and SCADA. The drive stands are operated from a separate control room with video cameras installed within the test cells to provide an overview of rig operation, as well as the GUI feed for control and data acquisition. There are a range of test instrumentation devices that can be integrated to both stand and research test unit, as well as high speed visualisation (including infra-red imaging for thermal considerations)
Single Test Shaft Facility (SSTF)
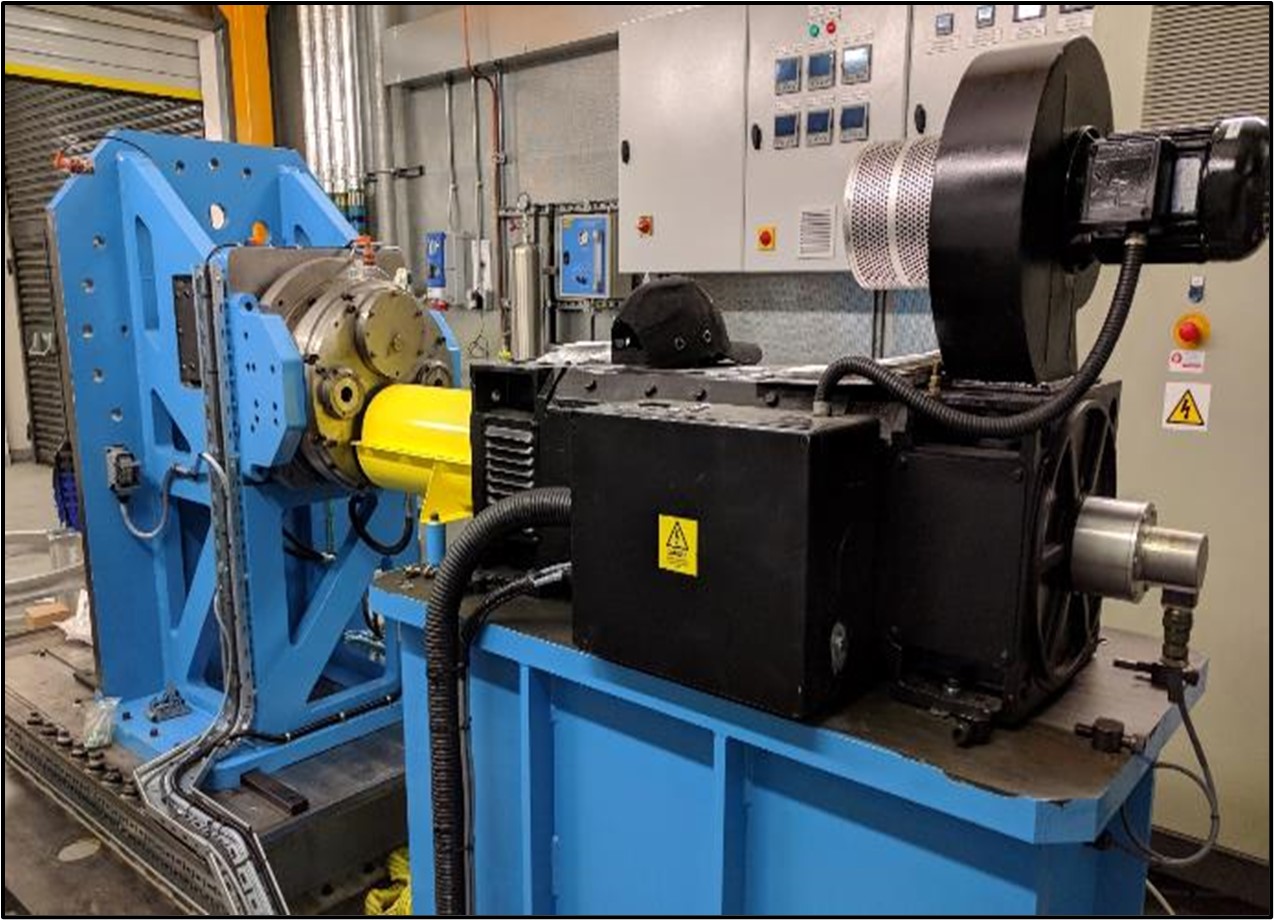
The SSTF has been used extensively to support investigations into, and modelling of, flowbehaviour and aeroengine bearing chambers. The facility has been designed to supportoverhung loads and can also include an integrated shaft seal and a 10 bar (max.)pressure vessel.
Main drive:
- 15,000 rpm and 180 kW
- Bulkhead designed for overheadloads and can include andintegrated shaft seal.
Oil systems:
- 160 lpm, 215 bar max
- 80 °C
- 6 feed control stations(0.06 lpm to 45 lpm)
DAQ:
- General purpose analogue input:10 V range, 100 mV range, 24bit, 51.2 kS/s, LP filtering.
- 32 thermocouple channels, 24bit, 1 to 90 S/s, LP filtering.
Two Shaft Test Facility (2STF)
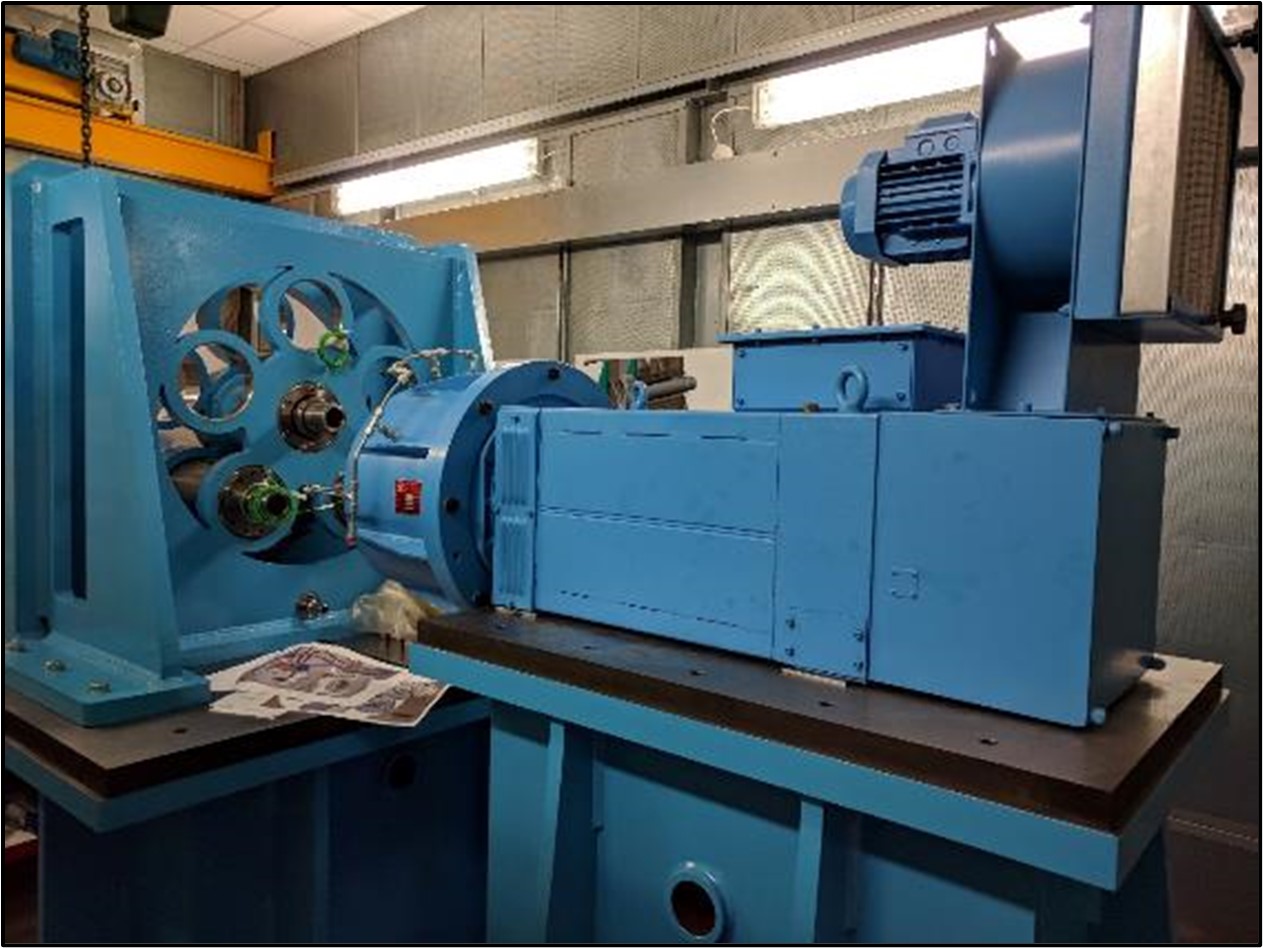
Each drive on the 2STF has similar capabilities as that of the SSTF; the drives can be used separately or co-axially. It has been used for investigations of oil behaviour and heat generation mechanisms under high loads, and it can be adapted to include visualisation of a test article.
Main drive:
- Drive 1: 15,000 rpm (+ direct), 138 kW
- Drive 2: 15,000 rpm (+ direct), 95 kW
- Power recirculation available
Oil systems:
- 160 lpm, 100 bar max.(power limited to 15 kW)
- 80 °C
- Up to six controlled feeds:
- Flow control: four valves currently fitted: 2x 0.06 - 45 lpm, 2x 0.085 - 65 lpm
- Pressure control available (up to max. pump pressure)
DAQ:
- General purpose analogue input: 10 V range, 100 mV range, 24 bit, 51.2 kS/s, LP filtering.
- 32 thermocouple channels, 24bit, 1 to 90 S/s, LP filtering.
Three Shaft Test Facility
The ATI-funded 3STF is a multi-purpose facility that has three shafts which can beoriented flexibly for investigations of different transmission system and componentphenomena. It has been used to investigate, among other things, hydraulic seals usedin intershaft seals as well as the effects of flowrates and oil jet geometries on bearingbehaviour and bearing chamber wall films & scavenge.
Main drive:
- Drive 1 & 2: 35,000 rpm, 290 kW
- Drive 3: 60,000 rpm, 62 kW
- Flexible orientation of drives
Oil systems Air Systems:
- 3 oil feeds:
- Two up to 60 l/min andone up to 100 l/min
- 120 °C (max.)
- Pressure or flow control
- 3 oil scavenges:
- Up to 175 l/min
- 240 °C (max.)
- Air/oil separation and measurement(up to 93% air volume fraction)
- 3 air feeds
-
- Up to 160 g/s
- 10 bar (max.)
- 2 air vents:
- Up to 200 g/s
- 10 bar (max.)
- Air/oil separation and measurement
DAQ:
- Dedicated TorDAQ system
- 16 analogue inputs and outputs
- 8 digital inputs and outputs